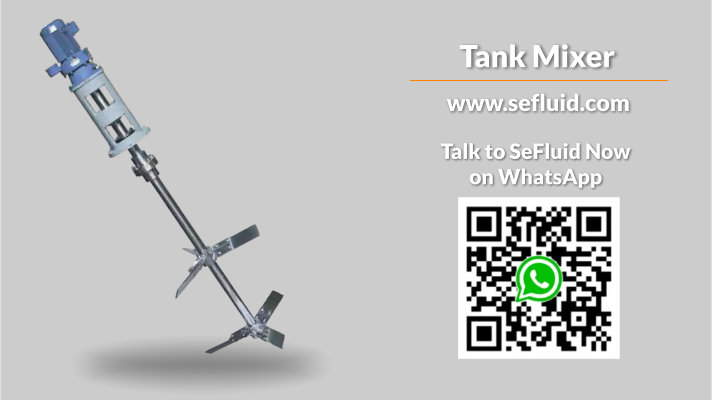
Introduction of Tank Mixer
Tank mixer is a mechanical device designed for effective blending and homogenization of fluids within large storage tanks. These mixers generally consist of a sturdy drive system connected to an impeller or agitator functioning inside the tank. They guarantee thorough mixing of liquids, suspensions, and slurries by initiating material movement, thus enhancing reactions, averting sedimentation, and preserving product uniformity. At SeFluid, we excel in crafting top-notch tank mixers tailored to a broad spectrum of process demands. Our mixers distinguish themselves through their outstanding durability, energy efficiency, and precise engineering. We focus on designing models that are user-friendly for maintenance and cleaning, while being fully customizable to accommodate various liquid viscosities and tank sizes. We produce our tank mixers using corrosion-resistant materials and strictly follow rigorous international safety norms such as ATEX and GMP, ensuring safe and reliable operation even under hazardous conditions. Our commitment to innovation leads us to integrate advanced control systems into our tank mixers, allowing for exact speed adjustment and optimum process outcomes. This unique combination of performance, dependability, and flexibility sets our tank mixers apart as a preferred choice for clients demanding the highest quality.Working Principle of Tank Mixer
The working principle of a tank mixer involves a systematic approach to effectively blend and homogenize the contents within a storage tank. The core components include a motor-driven mechanism and a mixing element, typically an impeller or agitator, submerged in the tank's liquid content. When operational, the motor supplies power to rotate the impeller or agitator at a predetermined speed. The impeller's design determines the flow pattern it creates within the tank. For instance, axial flow impellers induce a horizontal flow pattern, radial flow impellers create a vertical circulation, and pitched blade turbines provide a more turbulent and omnidirectional mixing action. The rotating impeller generates a series of vortices and currents which force the liquid to move throughout the tank volume. This continuous motion ensures that any settled solids are suspended and mixed evenly into the liquid. In cases where multiple phases are present (e.g., solid particles in a liquid suspension), the mixer helps prevent settling by keeping the mixture homogeneous. In essence, tank mixers work by converting the mechanical energy from the motor into fluid motion, promoting efficient blending and reaction kinetics, and maintaining product consistency over time. Depending on the application, they can be adjusted to achieve gentle mixing or powerful agitation to break down lumps or disperse substances thoroughly.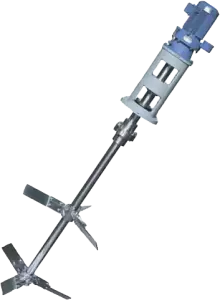
Specification
Power: 1.5-100 kw Capacity: 1.5-110 m³/h Material: SS304/SS316 RPM: 0-2930 Request for QuotationTypes of Tank Mixer
Tank mixers come in various types to address different mixing requirements across a wide range of industries. Here are some common types:- Propeller Mixers: These use a propeller-style impeller to create a rotational flow pattern, suitable for low to medium viscosity fluids. Propeller mixers can generate either laminar or turbulent flows depending on the pitch and diameter of the blades.
- Paddle Mixers: Ideal for viscous products and dry bulk solids, paddle mixers use flat, broad blades to push and fold the materials. They are often used for blending powders, granules, or pastes.
- Agitators: Agitators have several types of impellers, including turbine, anchor, helical ribbon, or pitched blade turbine. Turbine agitators generate high shear forces and are used for rapid blending, while anchor agitators create slow-moving, vertical currents ideal for suspending solids in liquids.
- Static Mixers: Unlike dynamic mixers, static mixers don't rely on moving parts. Instead, they use a sequence of stationary elements within the tank to split, redirect, and recombine the flow streams for thorough mixing.
- Jet Mixers: These mixers utilize high-velocity fluid jets to induce mixing. By injecting pressurized liquid into the tank, they create intense turbulence and promote rapid blending.
-
Magnetic Stirrers: Mainly used in laboratory settings, these mixers have a magnetic field generated outside the tank that rotates a magnetic stir bar inside, stirring the liquid contents.
- Emulsifying Mixers: Specialized mixers designed for emulsions or dispersions feature high-shear mixing heads that can break down droplets or particles to extremely small sizes.
SeFluid's Advantages on Tank Mixer Manufacturing
SeFluid distinguishes itself in the manufacturing of tank mixers through a multitude of advantages that reflect its commitment to innovation, quality, and customization: 1. Advanced Engineering: SeFluid employs cutting-edge technologies in the design and construction of its tank mixers. This includes precision-engineered impellers and agitation systems that ensure optimal fluid dynamics for enhanced mixing efficiency. 2. Durability & Efficiency: The company uses high-quality materials to build robust mixers that withstand harsh chemical environments and resist corrosion. Additionally, SeFluid's tank mixers are known for their energy efficiency, reducing operational costs and environmental impact. 3. Customizability: Recognizing that each application requires a unique solution, SeFluid offers a wide range of customizable tank mixers to accommodate various viscosities, tank volumes, and process requirements. Clients can choose from different impeller types, mounting options, and control systems to match their specific needs. 4. Compliance & Safety: All SeFluid tank mixers comply with industry-leading safety standards, such as ATEX and GMP, ensuring safe operation in potentially explosive atmospheres and meeting strict pharmaceutical manufacturing guidelines. 5. Service & Support: SeFluid provides comprehensive pre-sales consultation, installation support, and post-sales maintenance services to ensure that their tank mixers deliver consistent, reliable performance throughout their lifespan. 6. Intelligent Controls: SeFluid integrates state-of-the-art control systems into its tank mixers, allowing users to monitor and regulate mixing speed and intensity accurately, further optimizing process outcomes. By combining these strengths, SeFluid establishes itself as a trusted partner for businesses seeking innovative, high-performance, and reliable tank mixing solutions.Request for Quotation
Talk To Us
We strongly recommend that you either click or scan the QR code below to talk directly with our sales engineers so that we can help you find the most suitable products for your application needs.





NEWS
CONTACT US
No 10, Jinhai Rd, Hefei, China 201400 Phone: +86 156 6910 1862 Fax: +86 551 5843 6163 sales@sefluid.comFOLLOW US







