Introduction of Reaction Tank
Reaction tanks, also known as reaction vessels or reactors, are integral components in various industrial processes where chemical reactions take place. They serve as controlled environments for these reactions, ensuring optimal conditions for efficiency, safety, and product quality.
How Reaction Tank Works
A reaction tank is a crucial component in industrial processes where chemical reactions occur. Its primary function is to provide a controlled environment for these reactions, ensuring optimal conditions for efficiency, safety, and product quality. The following is an overview of how a reaction tank works:
- Reactant Inclusion: The process begins with the introduction of reactants into the reaction tank. These reactants can be in liquid, solid, or gaseous form, depending on the specific reaction being carried out. Accurate measurement and dosing of the reactants are essential to achieve the desired stoichiometry and prevent unwanted side reactions.
- Mixing and Agitation: Once the reactants are inside the tank, mixing and agitation mechanisms are employed to ensure homogeneous distribution and efficient interaction between the substances. This can be achieved through various methods, such as mechanical stirrers, impellers, baffles, or jet mixers. Proper mixing is crucial for enhancing reaction kinetics, improving heat transfer, and maintaining uniform temperature and concentration throughout the reaction mixture.
- Temperature Control: Temperature is a critical parameter in most chemical reactions, as it directly affects reaction rates and product yields. Reaction tanks are often equipped with heating or cooling systems to maintain the desired temperature during the reaction process. Heating jackets, cooling coils, or internal heating elements can be used to adjust and control the temperature within the tank.
- Pressure Control: Some reactions require specific pressure conditions to proceed efficiently or safely. Reaction tanks are designed to withstand the required pressure range and may incorporate features like pressure relief valves to manage and regulate internal pressure levels.
- Monitoring and Control: Throughout the reaction process, various parameters such as temperature, pressure, pH, and reactant concentrations are continuously monitored and controlled using sensors, instruments, and automation systems. This ensures that the reaction proceeds according to the desired conditions and helps operators make necessary adjustments to optimize the process.
- Reaction Progress: As the reaction progresses, the composition of the mixture inside the tank changes. Regular sampling and analysis of the reaction mixture help monitor the progress of the reaction, identify any deviations from the desired course, and make necessary adjustments to reactant feed rates, temperature, or other parameters.
- Termination and Product Recovery: Once the reaction has reached the desired endpoint, the process is terminated, and the product is recovered from the reaction tank. This can involve separation techniques such as filtration, centrifugation, or distillation, depending on the nature of the product and any byproducts generated during the reaction.
- Cleaning and Maintenance: After each use, reaction tanks must be thoroughly cleaned and inspected for any signs of wear or damage. Proper cleaning and maintenance procedures ensure the longevity and reliability of the equipment and prevent contamination in subsequent reactions.
In general, a reaction tank works by providing a controlled environment for chemical reactions to occur efficiently and safely. It facilitates the introduction and mixing of reactants, maintains optimal temperature and pressure conditions, monitors and controls reaction parameters, and enables product recovery and post-reaction cleaning. By understanding and optimizing the workings of a reaction tank, industries can enhance productivity, improve product quality, and maintain high levels of safety and environmental sustainability.
Functions of Reaction Tank
Reaction tanks are commonly used in various industrial processes, particularly in chemical engineering and wastewater treatment. These tanks serve several important functions depending on the specific application. Here are some common functions of reaction tanks:
- Mixing: Reaction tanks are primarily used for mixing different substances or chemicals. They provide an environment where the reactants can be thoroughly blended to initiate and facilitate chemical reactions. Mixing ensures that the reactants come into contact with each other, allowing for efficient reaction kinetics.
- Chemical Reactions: The main purpose of a reaction tank is to promote chemical reactions. It provides a controlled environment where reactants can interact and transform into desired products. The tank may contain catalysts, heat exchangers, or other additives to enhance the reaction rates or modify reaction conditions.
- Temperature Control: Reaction tanks often incorporate temperature control mechanisms to maintain the desired reaction temperature. Heat transfer devices, such as coils or jackets, are commonly used to either heat or cool the contents of the tank. Temperature control is crucial for achieving optimal reaction rates, selectivity, and overall process efficiency.
- Residence Time: Reaction tanks allow for a specific residence time, which refers to the duration for which the reactants remain in the tank. Residence time is critical for controlling the extent of reaction and achieving the desired conversion or yield. By adjusting the flow rate of reactants or the size of the tank, the residence time can be controlled.
- Separation: In some cases, reaction tanks are used in conjunction with separation processes. After the chemical reaction occurs, the tank may be equipped with separation mechanisms like settling, filtration, or centrifugation to separate the desired products from unreacted materials or by-products.
- pH Control: For reactions that are sensitive to pH, reaction tanks may include pH control systems. These systems monitor and adjust the pH level of the reaction mixture to maintain optimal reaction conditions. pH control is essential for achieving desired reaction rates, selectivity, and stability.
- Safety and Containment: Reaction tanks are designed to ensure safety during chemical reactions. They are constructed using materials that are compatible with the reactants and can withstand the process conditions. Additionally, they may have safety features like pressure relief valves, venting systems, or emergency shutdown mechanisms to prevent accidents or release of hazardous substances.
- Sampling and Analysis: Reaction tanks may include provisions for sampling the reaction mixture at various stages. These samples can be analyzed to monitor the progress of the reaction, determine reaction kinetics, or assess the quality of the products. Sampling and analysis help in process optimization and quality control.
It's important to note that the specific functions of a reaction tank can vary depending on the industry, application, and process requirements. The design and operation of reaction tanks are tailored to meet the specific needs of the chemical reaction or process being carried out.
SeFluid's Advantages on Manufacturing Reaction Tank
At SeFluid, we take pride in the numerous advantages we offer in the manufacturing of reaction tanks. With our extensive expertise and commitment to excellence, we provide exceptional solutions in this field. Here are some of the notable advantages that set us apart:
- Customized Design: We excel in creating customized designs that precisely meet the unique requirements of our clients. We understand that every manufacturing process is distinct, and we work closely with our clients to tailor the reaction tank to their specific needs.
- Engineering Expertise: Our team of experienced engineers possesses in-depth knowledge of reaction tank manufacturing. With expertise spanning various industries and applications, we provide valuable insights and recommendations to ensure optimal solutions that enhance efficiency and performance.
- Quality Assurance: Quality is at the core of our manufacturing process. We adhere to rigorous quality control procedures at every stage, ensuring that the reaction tanks we deliver meet the highest standards. By utilizing advanced techniques and conducting thorough inspections, we guarantee reliable and durable tanks that consistently perform.
- Advanced Materials: We understand the critical importance of selecting the most suitable materials for reaction tanks. Our expertise allows us to utilize advanced materials that are compatible with different manufacturing processes, offering resistance to corrosion, temperature fluctuations, and chemical reactions. This focus on material selection enhances the longevity and reliability of our tanks.
- Safety Considerations: Safety is our utmost priority when it comes to manufacturing reaction tanks. We incorporate various safety features into our tank designs, including pressure relief valves, emergency shutdown systems, and proper venting mechanisms. These precautions protect personnel, equipment, and the environment from potential hazards.
- Technological Innovation: Embracing technological advancements, we continuously improve our manufacturing processes. We stay updated with the latest industry trends and integrate innovative technologies into our tank designs. By leveraging automation, data analysis, and process optimization tools, we enhance efficiency, accuracy, and overall performance.
- Timely Delivery and Support: We understand the importance of meeting project deadlines. Our team is dedicated to delivering our reaction tanks on time without compromising on quality. Additionally, we provide comprehensive after-sales support, including installation assistance, maintenance guidance, and responsive customer service. Our commitment ensures a smooth and satisfactory experience for our clients.
In conclusion, our advantages in manufacturing reaction tanks lie in our ability to offer customized designs, engineering expertise, unwavering commitment to quality, advanced material selection, focus on safety, technological innovation, and reliable customer support. These advantages make us a trusted partner for companies seeking high-quality and tailored reaction tank solutions.
Applications of Reaction Tank
Reaction tanks find applications in various industries and processes where chemical reactions or mixing of substances are required. Some common applications of reaction tanks include:
- Chemical Manufacturing: Reaction tanks are extensively used in chemical manufacturing processes. They facilitate reactions such as polymerization, oxidation, reduction, esterification, and many others. These tanks provide controlled environments for the precise mixing of reactants and catalysts to produce desired chemical products.
- Pharmaceutical Production: In pharmaceutical manufacturing, reaction tanks play a crucial role in producing various drugs and pharmaceutical intermediates. They enable controlled reactions for synthesis, purification, and isolation of active pharmaceutical ingredients (APIs). Reaction tanks are used for processes like crystallization, hydrolysis, fermentation, and drug formulation.
- Petrochemical Industry: The petrochemical industry heavily relies on reaction tanks for the production of fuels, lubricants, polymers, and other petrochemical products. These tanks are used for processes like cracking, alkylation, isomerization, and polymerization, which involve complex chemical reactions and require precise control of reaction conditions.
- Food and Beverage Processing: Reaction tanks are employed in the food and beverage industry for various processes. They are used for fermentation in the production of alcoholic beverages, dairy products, and baked goods. Reaction tanks are also utilized for blending, flavoring, and chemical reactions involved in the production of processed foods and beverages.
- Water and Wastewater Treatment: In water and wastewater treatment plants, reaction tanks are used for various treatment processes. They facilitate chemical reactions for disinfection, pH adjustment, coagulation, flocculation, and precipitation of contaminants. These tanks help in removing impurities and ensuring the water or wastewater meets required quality standards.
- Environmental Remediation: Reaction tanks play a role in environmental remediation processes, where they are used to treat contaminated soil or water. They facilitate chemical reactions such as oxidation, reduction, and precipitation to transform or remove hazardous substances, pollutants, or heavy metals from the environment.
- Biotechnology and Biochemical Processes: Reaction tanks are vital in biotechnological and biochemical processes. They support fermentation processes for the production of biofuels, enzymes, antibiotics, and other bioproducts. These tanks provide optimal conditions for the growth of microorganisms or cell cultures and for the synthesis of desired compounds.
- Mining and Metallurgical Processes: Reaction tanks are utilized in mining and metallurgical industries for processes such as leaching, extraction, and ore processing. They enable chemical reactions to dissolve valuable metals from ores or concentrates, separate impurities, and recover metals through precipitation or electrochemical processes.
These are just a few examples of the diverse applications of reaction tanks. The specific use and design of a reaction tank depend on the desired chemical reactions, process conditions, and industry requirements.
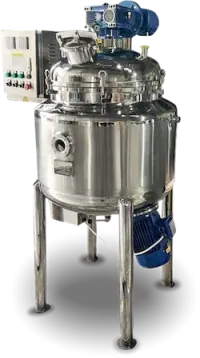
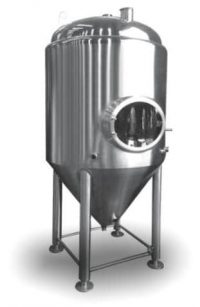

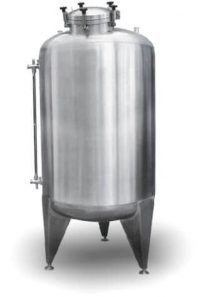
specification
Power
0.75-110 KW
Volume
0.03- 50000 L
Speed
Customized
Agitator Type
Top, Side, Bottom
Material
SS304, SS316, Carbon Steel
Temperature Control
Cooling, Heating, Insulation
Request for Quotation
Talk to us now !
We strongly recommend that you either click or scan the QR code below to talk directly with our sales engineers so that we can help you find the most suitable products for your application needs.


Telegram

Messenger

Viber


Skype
RELATED

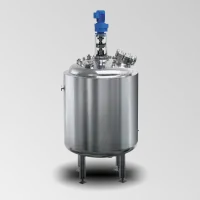
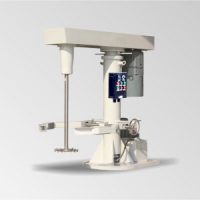
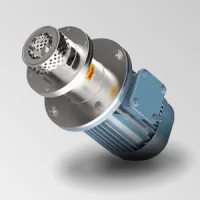




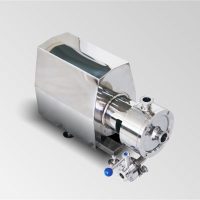

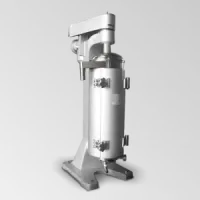

NEWS
CONTACT
No 10, Jinhai Rd, Hefei, China 201400
Phone: +86 156 6910 1862
Fax: +86 551 5843 6163
sales@sefluid.com
FOLLOW US




